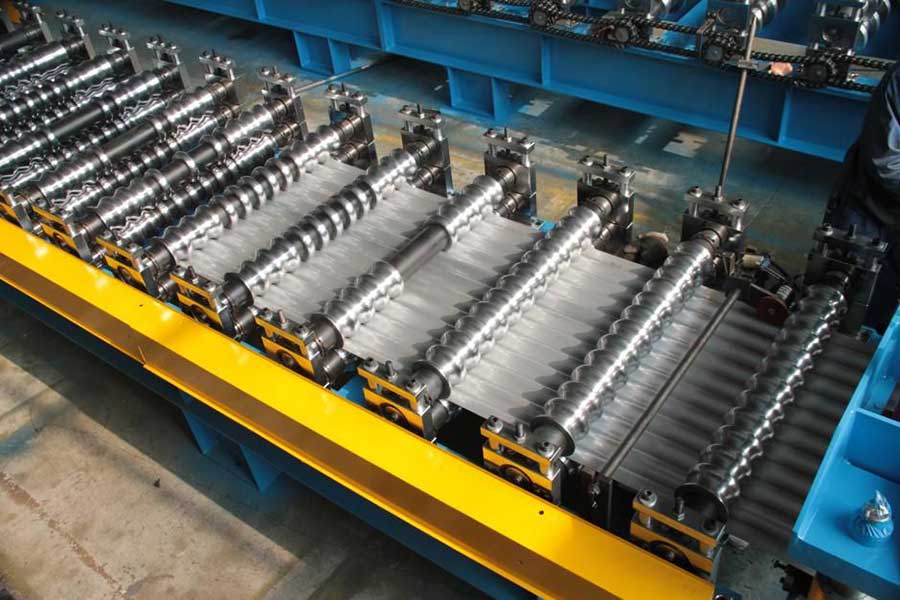
The working principle of roll forming machines represents one of the most elegant and effective methods in the world of metal forming. These machines perform the art of transforming flat strips of metal into complex and continuous profiles. Roll forming is almost like a metal ballet show; Step by step, the metal strip takes on the desired shape as it passes through a series of precisely designed form-giving rollers in the role of a "dancer". This process is based on a gradual and controlled deformation, rather than sudden and coercive forces, which makes it both gentle and powerful.
Cornerstones of the Roll Forming Process:
To understand the roll forming process, it is necessary to closely examine the basic components and stages of this process:
- Material Feeding Unit (Uncoiler): Like the beginning of any good performance, roll forming starts with the material. The metal strip wound into coils is placed in the unit called the uncoiler. This unit unwinds the metal strip in a controlled manner, ensuring a continuous and regular flow of material to the forming line. By adjusting the tension and speed of the metal, the opener creates the ideal starting conditions for the next stages.
- Forming Rollers (Roll Sets): The heart of roll forming is the forming rollers. These are precision-machined steel cylinders that carry the inverse of the final shape that will form the profile. A roll forming machine usually consists of a series of successive sets of rollers. Each set applies a slight shape change to the metal strip. The first sets subject the metal to pre-bending processes, while the later sets gradually deepen the profile even more, and the final sets give the final shape. The design of the rollers is done with great care according to the complexity of the profile to be produced and the precision requirements.
- Drive System: The power that enables the flow of the metal strip between the rollers and performs the forming process is produced by the drive system. Usually, rollers are rotated by means of electric motors and gearboxes. The drive system also performs important functions such as speed control and synchronization, ensuring that all roller sets work in harmony. This is critical for the profile to be formed properly and without errors.
- Guiding Systems: The correct and constant path of the metal strip along the forming line is vital for profile quality. Guiding systems precisely guide the metal strip between the rollers and prevent side movements, ensuring that the profile remains within the desired tolerances. These systems become even more important, especially in complex profiles and at high speeds.
- Cut-off System: After the forming process is completed, the continuous profile must be cut to the desired lengths. The cutting unit performs the cutting process quickly and precisely, without stopping the flow of the profile. Different cutting methods (flying saw, hydraulic shears, etc.) can be used. The cutting unit is usually integrated with a measuring system that precisely controls the length of the profile.
Step-by-Step Roll Forming Process:
The working principle of the roll forming machine consists of the following basic steps:
- Material Feeding: The coiled metal strip is placed in the opener and advanced towards the forming line in a controlled manner.
- Preforming: When the metal strip enters the first sets of rollers, light bends and pre-forming processes begin. This stage allows the metal to be prepared for the next stages and reduces the risk of cracking or wrinkling.
- Gradual Forming: As the metal strip moves on to the next sets of rollers, each set makes the shape of the profile more prominent step by step. The design of the rollers is optimized according to the complexity of the profile. For example, to create a U-shaped profile, rollers gradually bend the metal inward.
- Final Forming and Calibration: Final roller sets give the profile its final shape and ensure that the desired tolerances are achieved. At this stage, the accuracy of the dimensions and angles of the profile is checked and, if necessary, calibration procedures are performed.
- Cutting Process: The formed continuous profile reaches the cutting unit. Here, by cutting into predetermined lengths, the final products are obtained. The cut pieces are usually directed to a stacking unit.
Summary of the Basic Working Principle of Roll Forming:
The basic working principle of roll forming is based on gradual and continuous forming. As the metal strip passes through a series of rollers, each set of rollers applies a small shape change to the metal. This gradual approach makes it possible to produce the desired complex profiles with high speed and precision, without applying sudden and excessive force to the metal.
Advantages arising from the working principle:
The working principle of roll forming brings with it a number of important advantages:
- Continuous Production: Roll forming is a continuous process. The metal strip passes through the forming line without interruption, which means high production speeds and efficiency.
- Profile Consistency: The precise design of the rollers and the continuous process ensure that the sizes and shapes of the profiles produced are extremely consistent. This is especially important in applications that require assembly.
- Material Efficiency: Roll forming minimizes the wastage rate by using the material effectively. This reduces costs and reduces environmental impact.
- Variety and Flexibility: Different profile shapes and materials can be processed by roll forming. Different profiles can be produced by changing the roller sets, which provides production flexibility.
As a result, the working principle of roll forming machines is a point where engineering intelligence and precision meet. The stepped forming approach offers a unique method for transforming metal strips into complex and precise profiles. This principle has made roll forming an indispensable production technology of modern industry.